합판은 3개 이상의 얇은 목재 층을 접착제로 접착하여 만듭니다.목재의 각 층 또는 합판은 일반적으로 수축을 줄이고 완성된 조각의 강도를 향상시키기 위해 결이 인접한 층과 직각을 이루도록 방향이 지정됩니다.대부분의 합판은 건축에 사용되는 크고 평평한 시트로 압축됩니다.다른 합판 조각은 가구, 보트 및 항공기에 사용하기 위해 단순 곡선 또는 복합 곡선으로 형성될 수 있습니다.
건축 수단으로 얇은 나무 층을 사용한 것은 대략 기원전 1500년으로 거슬러 올라갑니다. 그때 이집트 장인들이 얇은 흑단 나무 조각을 투트-앙크-아몬 왕의 무덤에서 발견된 삼나무 상자 외부에 접착했습니다.이 기술은 나중에 그리스인과 로마인이 고급 가구와 기타 장식품을 생산하는 데 사용되었습니다.1600년대에는 얇은 나무 조각으로 가구를 장식하는 기술이 베니어링으로 알려졌고, 조각 자체도 베니어로 알려지게 되었습니다.
1700년대 후반까지 베니어 조각은 모두 손으로 절단되었습니다.1797년 영국인 사무엘 벤담(Samuel Bentham) 경은 베니어판을 생산하는 여러 기계에 대한 특허를 신청했습니다.그는 특허 출원서에서 접착제로 여러 겹의 베니어를 적층하여 더 두꺼운 조각을 만드는 개념을 설명했는데, 이는 현재 우리가 합판이라고 부르는 것에 대한 첫 번째 설명입니다.
이러한 발전에도 불구하고 적층 베니어판이 가구 산업 이외의 상업적 용도로 사용되기까지는 거의 100년이 걸렸습니다.1890년경에 합판 목재가 처음으로 문을 만드는 데 사용되었습니다.수요가 증가함에 따라 여러 회사에서 문용뿐만 아니라 철도 차량, 버스 및 비행기에 사용되는 여러 겹의 합판 목재 시트를 생산하기 시작했습니다.이러한 사용 증가에도 불구하고 일부 장인이 비꼬듯 "붙인 목재"를 사용한다는 개념은 제품에 대한 부정적인 이미지를 생성했습니다.이러한 이미지에 대응하기 위해 적층 목재 제조업체들은 새로운 재료를 설명하기 위해 "합판"이라는 용어를 만나 최종적으로 합의했습니다.
1928년에 일반 건축 자재로 사용하기 위해 최초의 표준 크기 4피트 x 8피트(1.2m x 2.4m) 합판 시트가 미국에 도입되었습니다.이후 수십 년 동안 개선된 접착제와 새로운 생산 방법으로 인해 합판을 다양한 용도로 사용할 수 있게 되었습니다.오늘날 합판은 다양한 건축 목적으로 절단 목재를 대체했으며 합판 제조는 전 세계적으로 수십억 달러 규모의 산업이 되었습니다.
합판의 바깥층은 각각 앞면과 뒷면으로 알려져 있습니다.얼굴은 사용되거나 보여지는 표면인 반면, 뒷면은 사용되지 않거나 숨겨져 있습니다.중앙 레이어를 코어라고 합니다.5겹 이상의 합판에서는 중간층을 크로스밴드라고 합니다.
합판은 활엽수, 연목 또는 이 둘을 조합하여 만들 수 있습니다.일반적인 활엽수로는 재, 단풍나무, 마호가니, 참나무, 티크 등이 있습니다.미국에서 합판을 만드는 데 사용되는 가장 일반적인 침엽수는 더글라스 전나무이지만 여러 종류의 소나무, 삼나무, 가문비나무, 레드우드도 사용됩니다.
복합 합판은 파티클보드 또는 가장자리가 연결된 단단한 목재 조각으로 만들어진 코어를 가지고 있습니다.앞면과 뒷면은 합판 베니어로 마감 처리되어 있습니다.매우 두꺼운 시트가 필요한 경우에는 복합 합판이 사용됩니다.
목재 층을 서로 접착하는 데 사용되는 접착제 유형은 완성된 합판의 특정 용도에 따라 다릅니다.건축물 외부 설치용 침엽수 합판 시트는 강도와 습기에 대한 저항성이 우수하기 때문에 일반적으로 페놀-포름알데히드 수지를 접착제로 사용합니다.구조물 내부 설치용으로 설계된 침엽수 합판 시트는 혈액 단백질 또는 대두 단백질 접착제를 사용할 수 있지만 현재 대부분의 침엽수 내부 시트는 외부 시트에 사용되는 것과 동일한 페놀-포름알데히드 수지로 만들어집니다.인테리어 용도와 가구 제작에 사용되는 견목 합판은 일반적으로 요소-포름알데히드 수지로 만들어집니다.
일부 응용 분야에서는 외부 표면에 습기 및 마모에 대한 추가적인 저항력을 부여하거나 페인트를 개선하기 위해 얇은 플라스틱, 금속 또는 수지 함침 종이나 천을 앞면이나 뒷면(또는 둘 다)에 접착한 합판 시트가 필요합니다. 재산을 보유하고 있습니다.이러한 합판을 중첩합판이라고 하며 건설, 운송, 농업 산업에서 흔히 사용됩니다.
다른 합판 시트는 액체 얼룩으로 코팅하여 표면을 마감 처리하거나 다양한 화학 물질로 처리하여 합판의 난연성 또는 부식 저항성을 향상시킬 수 있습니다.
합판에는 두 가지 종류가 있으며 각각 고유한 등급 시스템이 있습니다.
한 클래스는 건설 및 산업으로 알려져 있습니다.이 등급의 합판은 주로 강도 때문에 사용되며 노출 성능과 앞면과 뒷면에 사용되는 베니어 등급에 따라 평가됩니다.노출 기능은 접착제 유형에 따라 내부 또는 외부일 수 있습니다.베니어 등급은 N, A, B, C 또는 D일 수 있습니다. N 등급은 표면 결함이 거의 없는 반면, D 등급은 옹이와 갈라짐이 많을 수 있습니다.예를 들어, 주택 바닥재로 사용되는 합판은 "인테리어 CD" 등급을 받습니다.즉, 앞면은 C이고 뒷면은 D이며 접착제는 보호된 위치에 사용하기에 적합합니다.모든 건축용 합판과 산업용 합판의 내부 층은 등급에 관계없이 C등급 또는 D등급 베니어로 만들어집니다.
다른 종류의 합판은 견목 및 장식용 합판으로 알려져 있습니다.이 등급의 합판은 주로 외관을 위해 사용되며 내습성 순서에 따라 기술(외부), 유형 I(외부), 유형 II(내부), 유형 III(내부)로 등급이 지정됩니다.페이스 베니어판에는 사실상 결함이 없습니다.
크기
합판 시트의 두께는 다음과 같습니다.1.6mm(06인치) ~ 76mm(3.0인치)가장 일반적인 두께는 0.25인치(6.4mm) ~ 0.75인치(19.0mm) 범위입니다.코어, 크로스밴드, 합판의 앞면과 뒷면은 서로 다른 두께의 베니어로 만들어질 수 있지만 각각의 두께는 중심을 중심으로 균형을 이루어야 합니다.예를 들어, 얼굴과 뒷면의 두께가 동일해야 합니다.마찬가지로 상단 및 하단 크로스밴드도 동일해야 합니다.
건축에 사용되는 합판 시트의 가장 일반적인 크기는 너비 4피트(1.2m), 길이 8피트(2.4m)입니다.다른 일반적인 너비는 3피트(0.9m)와 5피트(1.5m)입니다.길이는 8피트(2.4m)부터 12피트(3.6m)까지 1피트(0.3m) 단위로 다양합니다.보트 건조와 같은 특수 용도에는 더 큰 시트가 필요할 수 있습니다.
합판을 만드는 데 사용되는 나무는 일반적으로 목재를 만드는 데 사용되는 나무보다 직경이 더 작습니다.대부분의 경우 합판 회사가 소유한 지역에 심고 재배했습니다.이 지역은 나무 성장을 극대화하고 곤충이나 화재로 인한 피해를 최소화하기 위해 신중하게 관리됩니다.
다음은 나무를 표준 4피트 x 8피트(1.2m x 2.4m) 합판 시트로 가공하기 위한 일반적인 작업 순서입니다.
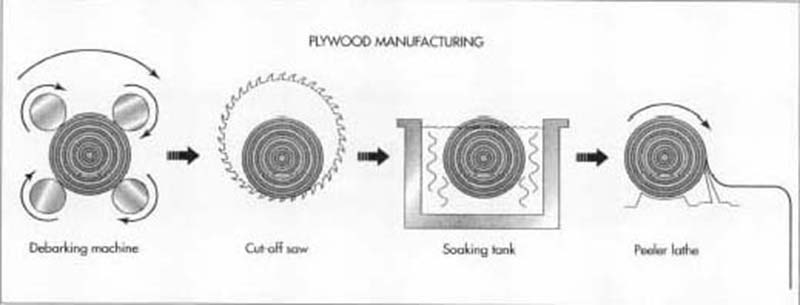
먼저 통나무의 껍질을 벗긴 다음 필러 블록으로 자릅니다.블록을 베니어 스트립으로 자르려면 먼저 담근 다음 스트립으로 벗겨냅니다.
1 한 지역에서 선택한 나무는 자르거나 벌채할 준비가 된 것으로 표시됩니다.벌목은 휘발유 동력 사슬톱을 사용하거나 펠러라고 불리는 바퀴 달린 차량의 전면에 장착된 대형 유압 가위를 사용하여 수행할 수 있습니다.쓰러진 나무의 사지는 전기톱으로 제거됩니다.
2 손질된 나무 줄기 또는 통나무는 스키더라고 불리는 바퀴 달린 차량에 의해 적재 장소로 끌려갑니다.통나무는 길이에 맞게 절단되어 합판 공장으로 이동하기 위해 트럭에 실려 통나무 데크라고 알려진 긴 더미로 쌓여 있습니다.
3 통나무가 필요하면 고무 타이어 로더를 사용하여 통나무 데크에서 픽업한 후 껍질 제거 기계로 가져오는 체인 컨베이어에 놓습니다.이 기계는 날카로운 톱니가 있는 연삭 휠이나 고압 물 분사기를 사용하여 나무껍질을 제거하며, 이때 통나무는 장축을 중심으로 천천히 회전합니다.
4 껍질이 벗겨진 통나무는 거대한 원형 톱이 약 8피트-4인치(2.5m)에서 8피트-6인치(2.6m) 길이의 섹션으로 절단되는 체인 컨베이어를 통해 제재소로 운반됩니다. 이는 표준 8피트 제조에 적합합니다. (2.4m) 긴 시트.이러한 로그 섹션을 필러 블록이라고 합니다.
5 베니어판을 절단하기 전에 필러 블록을 가열하고 담가서 목재를 부드럽게 해야 합니다.블록은 찌거나 뜨거운 물에 담글 수 있습니다.이 과정은 목재 종류, 블록 직경 및 기타 요인에 따라 12~40시간이 소요됩니다.
6 가열된 필러 블록은 필러 선반으로 운반되어 자동으로 정렬되어 한 번에 하나씩 선반에 공급됩니다.선반이 장축을 중심으로 블록을 빠르게 회전시키면 전체 길이의 칼날이 300-800피트/분(90-240m/분)의 속도로 회전 블록 표면에서 연속 베니어 시트를 벗겨냅니다.블록의 직경이 약 230~305mm(3~4인치)로 줄어들면 필러 코어로 알려진 남은 나무 조각이 선반에서 배출되고 새 필러 블록이 제자리에 공급됩니다.
7 필러 선반에서 나오는 긴 베니어 시트는 즉시 처리될 수도 있고, 긴 다단 트레이에 보관되거나 롤에 감길 수도 있습니다.어쨌든 다음 공정에서는 표준 1.2m(4피트) 너비 합판 시트를 만들기 위해 베니어를 사용 가능한 너비(보통 약 1.4m)로 절단하는 작업이 포함됩니다.동시에 광학 스캐너는 허용할 수 없는 결함이 있는 부분을 찾아 잘라내고 표준 너비보다 작은 베니어 조각만 남깁니다.
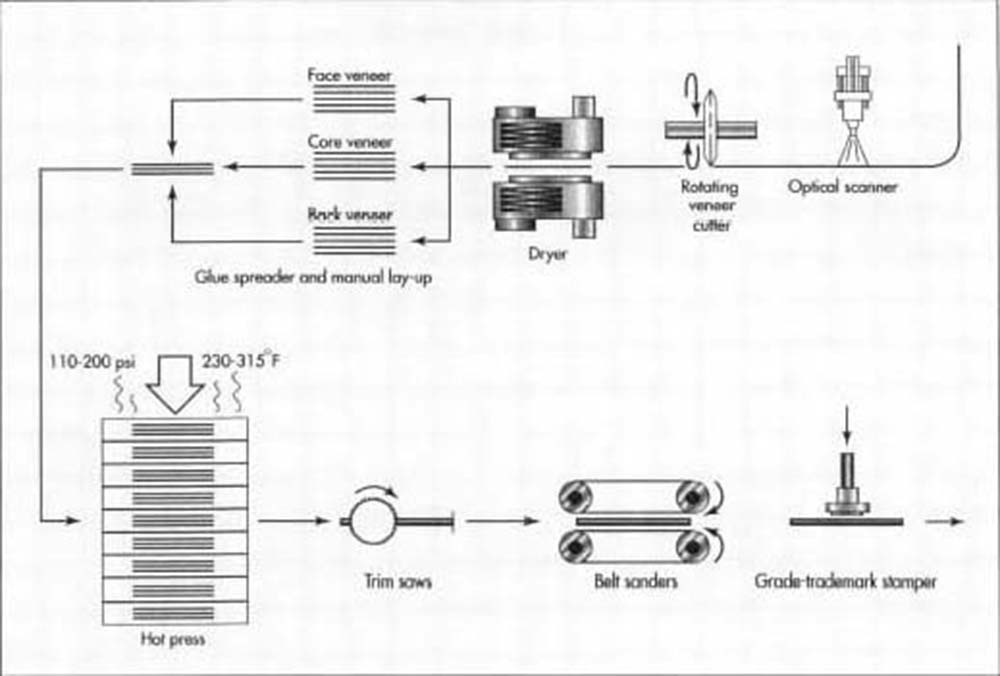
젖은 베니어판을 롤 모양으로 감으면 광학 스캐너가 목재에서 허용할 수 없는 결함을 감지합니다.일단 건조되면 베니어는 등급이 매겨지고 쌓입니다.선택한 베니어 부분이 서로 접착됩니다.뜨거운 프레스를 사용하여 베니어를 하나의 단단한 합판 조각으로 밀봉하고 적절한 등급으로 스탬프를 찍기 전에 다듬고 샌딩합니다.
8 그런 다음 베니어 섹션을 등급에 따라 분류하고 쌓습니다.이는 수동으로 수행할 수도 있고 광학 스캐너를 사용하여 자동으로 수행할 수도 있습니다.
9 분류된 부분을 건조기에 넣어 수분 함량을 줄이고 접착되기 전에 수축되도록 합니다.대부분의 합판 공장에서는 조각이 가열된 챔버를 통해 지속적으로 이동하는 기계식 건조기를 사용합니다.일부 건조기에서는 고속의 가열된 공기 제트가 조각 표면을 가로질러 불어 건조 과정을 가속화합니다.
10 건조기에서 베니어 조각이 나오면 등급에 따라 쌓입니다.폭이 작은 부분에는 테이프나 접착제로 접합된 추가 베니어가 있어 외관과 강도가 덜 중요한 내부 레이어에 사용하기에 적합합니다.
11 가로로 설치될 베니어 부분(3겹 시트의 코어 또는 5겹 시트의 크로스밴드)은 약 1.3m(4피트-3인치) 길이로 절단됩니다.
12 특정 합판을 위해 적절한 베니어 부분이 조립되면 조각들을 서로 붙이고 붙이는 과정이 시작됩니다.이는 수동으로 수행되거나 기계를 사용하여 반자동으로 수행될 수 있습니다.3겹 시트의 가장 간단한 경우 뒷면 베니어는 평평하게 놓여지고 접착제 스프레더를 통과하여 윗면에 접착제 층을 도포합니다.그런 다음 코어 베니어의 짧은 부분을 접착된 뒷면 위에 십자형으로 놓고 전체 시트를 두 번째로 접착 스프레더를 통해 통과시킵니다.마지막으로, 접착된 코어 위에 페이스 베니어를 놓고 시트는 인쇄기에 들어가기를 기다리는 다른 시트와 함께 쌓입니다.
13 접착 시트는 다중 개방형 핫 프레스에 로드됩니다.인쇄기는 한 번에 20~40매를 처리할 수 있으며 각 시트는 별도의 슬롯에 로드됩니다.모든 시트가 로드되면 프레스는 약 110-200psi(7.6-13.8bar)의 압력으로 시트를 함께 압착하는 동시에 약 230-315°F(109.9-157.2°F)의 온도로 가열합니다. 씨).압력은 베니어 층 사이의 양호한 접촉을 보장하고 열은 최대 강도를 위해 접착제가 적절하게 경화되도록 합니다.2~7분 후에 프레스가 열리고 시트가 배출됩니다.
14 거친 시트는 일련의 톱을 통과하여 최종 너비와 길이로 다듬어집니다.고급 시트는 1.2m(4피트) 폭의 벨트 샌더 세트를 통과하여 앞면과 뒷면을 모두 샌딩합니다.중간 등급 시트는 거친 부분을 청소하기 위해 수동으로 부분 샌딩 처리됩니다.일부 시트는 원형 톱날 세트를 통과하여 표면의 얕은 홈을 잘라 합판에 질감 있는 모양을 부여합니다.최종 점검 후 남아있는 결함은 모두 수리됩니다.
15 완성된 시트에는 구매자에게 노출 등급, 등급, 밀 번호 및 기타 요소에 대한 정보를 제공하는 등급 상표가 찍혀 있습니다.동일한 등급의 상표가 있는 시트는 묶음으로 묶여 창고로 이동되어 배송을 기다립니다.
목재와 마찬가지로 완벽한 합판도 없습니다.모든 합판 조각에는 일정량의 결함이 있습니다.이러한 결함의 수와 위치에 따라 합판 등급이 결정됩니다.건축 및 산업용 합판에 대한 표준은 미국표준국(National Bureau of Standards)과 미국합판협회(American Plywood Association)가 마련한 제품 표준 PS1에 의해 정의됩니다.활엽수 및 장식용 합판에 대한 표준은 미국 국립 표준 협회(American National Standards Institute) 및 활엽수 합판 제조 협회(Hardwood Plywood Manufacturer' Association)에서 마련한 ANSIIHPMA HP에 의해 정의됩니다.이러한 표준은 합판의 등급 시스템을 확립할 뿐만 아니라 구조, 성능 및 적용 기준도 지정합니다.
합판이 나무를 상당히 효율적으로 사용하더라도(본질적으로 나무를 분해하고 더 강력하고 사용하기 쉬운 구성으로 다시 조립하는 것) 제조 공정에는 여전히 상당한 낭비가 내재되어 있습니다.대부분의 경우 나무에 사용 가능한 목재량의 약 50~75%만이 합판으로 전환됩니다.이 수치를 개선하기 위해 몇 가지 새로운 제품이 개발 중입니다.
한 가지 신제품은 방향성 스트랜드 보드(Oriented Strand Board)라고 하는데, 이는 통나무에서 베니어판을 벗겨내고 심지를 버리는 것이 아니라 통나무 전체를 가닥으로 파쇄하여 만든 것입니다.가닥은 접착제와 혼합되어 결이 한 방향으로 흐르도록 층으로 압축됩니다.이렇게 압축된 층은 합판처럼 서로 직각으로 배열되어 서로 접착됩니다.방향성 스트랜드 보드는 합판만큼 강하고 비용도 약간 저렴합니다.
게시 시간: 2021년 8월 10일