합판은 세 겹 이상의 얇은 목재 층을 접착제로 접합하여 만듭니다. 각 목재 층, 즉 합판은 일반적으로 나무결이 인접한 층에 직각을 이루도록 배열되어 수축을 줄이고 완성된 제품의 강도를 향상시킵니다. 대부분의 합판은 건축 자재로 사용되는 크고 평평한 판 형태로 압착됩니다. 다른 합판 조각들은 가구, 보트, 항공기에 사용하기 위해 단순 또는 복합 곡선으로 가공될 수 있습니다.
얇은 나무 층을 건축 자재로 사용한 것은 기원전 1500년경으로 거슬러 올라갑니다. 당시 이집트 장인들은 투탕카멘 왕의 무덤에서 발견된 삼나무 관의 외벽에 짙은 흑단 나무의 얇은 조각을 붙였습니다. 이 기법은 이후 그리스와 로마에서 고급 가구와 기타 장식품을 제작하는 데 사용되었습니다. 1600년대에는 얇은 나무 조각으로 가구를 장식하는 예술을 베니어링(veneering)이라고 부르게 되었고, 베니어는 베니어(veneer)로 알려지게 되었습니다.
1700년대 후반까지 베니어는 전적으로 수작업으로 절단되었습니다. 1797년, 영국인 새뮤얼 벤담 경은 베니어 생산을 위한 여러 기계에 대한 특허를 출원했습니다. 그는 특허 출원서에서 접착제를 사용하여 여러 겹의 베니어를 적층하여 더 두꺼운 판재를 만드는 개념을 설명했는데, 이는 오늘날 우리가 합판이라고 부르는 것에 대한 최초의 설명이었습니다.
이러한 발전에도 불구하고, 적층 베니어가 가구 산업 이외의 상업적 용도로 사용되기까지는 거의 100년이 더 걸렸습니다. 1890년경, 적층 목재는 처음으로 문 제작에 사용되었습니다. 수요가 증가함에 따라 여러 회사에서 문뿐만 아니라 철도 차량, 버스, 비행기에도 사용할 수 있도록 여러 겹의 적층 목재를 생산하기 시작했습니다. 이러한 사용 증가에도 불구하고, 일부 장인들이 비꼬는 표현처럼 "페이스트드 우드(pasted woods)"를 사용한다는 개념은 제품에 대한 부정적인 이미지를 만들어냈습니다. 이러한 이미지를 상쇄하기 위해 적층 목재 제조업체들은 모여 마침내 이 새로운 소재를 "합판(plywood)"이라는 용어로 명명하기로 결정했습니다.
1928년, 미국에서 최초로 표준 규격인 4피트 x 8피트(1.2m x 2.4m) 합판이 일반 건축 자재로 출시되었습니다. 이후 수십 년 동안 접착제의 개량과 새로운 생산 방식의 발전으로 합판은 다양한 용도로 사용될 수 있게 되었습니다. 오늘날 합판은 여러 건축 용도에서 기존 목재를 대체하고 있으며, 합판 제조는 전 세계적으로 수십억 달러 규모의 산업으로 성장했습니다.
합판의 바깥층은 각각 앞면과 뒷면이라고 합니다. 앞면은 사용하거나 보이는 표면이고, 뒷면은 사용하지 않거나 숨겨져 있습니다. 가운데 층은 코어라고 합니다. 5겹 이상의 합판에서는 중간층을 크로스밴드라고 합니다.
합판은 경재, 연재, 또는 이 두 가지를 혼합하여 만들 수 있습니다. 일반적인 경재로는 물푸레나무, 단풍나무, 마호가니, 참나무, 티크나무 등이 있습니다. 미국에서 합판을 만드는 데 가장 흔히 사용되는 연재는 더글러스 전나무이지만, 소나무, 삼나무, 가문비나무, 레드우드 등 여러 품종도 사용됩니다.
합성 합판은 파티클보드나 단단한 목재 조각을 모서리끼리 접합하여 만든 심재입니다. 겉면과 뒷면은 합판 베니어로 마감 처리되어 있습니다. 합성 합판은 매우 두꺼운 판재가 필요한 곳에 사용됩니다.
목재 층을 접합하는 데 사용되는 접착제의 종류는 완성된 합판의 특정 용도에 따라 달라집니다. 구조물 외부에 설치하도록 설계된 연목 합판 시트는 일반적으로 뛰어난 강도와 내습성을 가진 페놀-포름알데히드 수지를 접착제로 사용합니다. 구조물 내부에 설치하도록 설계된 연목 합판 시트는 혈액 단백질이나 대두 단백질 접착제를 사용할 수 있지만, 대부분의 연목 내부 시트는 현재 외부 시트에 사용되는 것과 동일한 페놀-포름알데히드 수지로 만들어집니다. 실내 및 가구 제작에 사용되는 경목 합판은 일반적으로 요소-포름알데히드 수지로 만들어집니다.
일부 용도에서는 플라스틱, 금속 또는 수지가 함침된 종이나 직물을 얇은 층으로 표면에 접착한 합판 시트가 필요합니다. 이러한 합판은 외부 표면의 습기 및 마모 저항성을 강화하거나 페인트 유지력을 향상시키기 위해 앞면이나 뒷면(또는 양쪽 모두)에 접착됩니다. 이러한 합판을 오버레이 합판이라고 하며, 건설, 운송, 농업 분야에서 일반적으로 사용됩니다.
합판 시트 중에는 표면에 마감된 모양을 주기 위해 액상 염색제를 칠한 것도 있고, 합판의 내화성이나 부패 저항성을 높이기 위해 다양한 화학 물질로 처리한 것도 있습니다.
합판에는 두 가지 종류가 있으며, 각각 고유한 등급 시스템이 있습니다.
한 등급은 건설 및 산업용입니다. 이 등급의 합판은 주로 강도를 고려하여 사용되며, 노출 강도와 표면 및 뒷면에 사용된 베니어의 등급에 따라 등급이 매겨집니다. 노출 강도는 접착제 종류에 따라 내부 또는 외부로 구분됩니다. 베니어 등급은 N, A, B, C 또는 D로 구분됩니다. N 등급은 표면 결함이 거의 없는 반면, D 등급은 옹이와 갈라짐이 많을 수 있습니다. 예를 들어, 주택의 바닥재로 사용되는 합판은 "내부 CD" 등급입니다. 이는 표면이 C이고 뒷면이 D이며, 접착제는 보호 구역에서 사용하기에 적합하다는 것을 의미합니다. 모든 건설 및 산업용 합판의 내부 층은 등급과 관계없이 C 또는 D 등급 베니어로 제작됩니다.
합판의 다른 종류는 경재 및 장식용 합판입니다. 이 종류의 합판은 주로 외관을 위해 사용되며, 내습성에 따라 기술 등급(외부용), 유형 I 등급(외부용), 유형 II 등급(내부용), 유형 III 등급(내부용)으로 분류됩니다. 표면 베니어는 거의 결함이 없습니다.
사이즈
합판 시트의 두께는 0.06인치(1.6mm)에서 3.0인치(76mm)까지 다양합니다. 가장 일반적인 두께는 0.25인치(6.4mm)에서 0.75인치(19.0mm) 사이입니다. 합판 시트의 중심부, 크로스밴드, 그리고 앞면과 뒷면은 서로 다른 두께의 베니어로 만들어질 수 있지만, 각 베니어의 두께는 중앙을 기준으로 균형을 이루어야 합니다. 예를 들어, 앞면과 뒷면의 두께는 동일해야 합니다. 마찬가지로 상단과 하단 크로스밴드의 두께도 동일해야 합니다.
건축 자재에 사용되는 합판의 가장 일반적인 크기는 폭 4피트(1.2m), 길이 8피트(2.4m)입니다. 다른 일반적인 폭으로는 폭 3피트(0.9m)와 길이 5피트(1.5m)가 있습니다. 길이는 8피트(2.4m)에서 12피트(3.6m)까지 1피트(0.3m) 단위로 다양합니다. 조선과 같은 특수 용도에는 더 큰 합판이 필요할 수 있습니다.
합판 제작에 사용되는 나무는 일반적으로 목재 제작에 사용되는 나무보다 지름이 작습니다. 대부분의 경우, 합판 회사 소유 지역에 심고 재배합니다. 이러한 지역은 나무 성장을 극대화하고 해충이나 화재 피해를 최소화하기 위해 세심하게 관리됩니다.
다음은 나무를 표준 4피트 x 8피트(1.2m x 2.4m) 합판 시트로 가공하는 일반적인 작업 순서입니다.
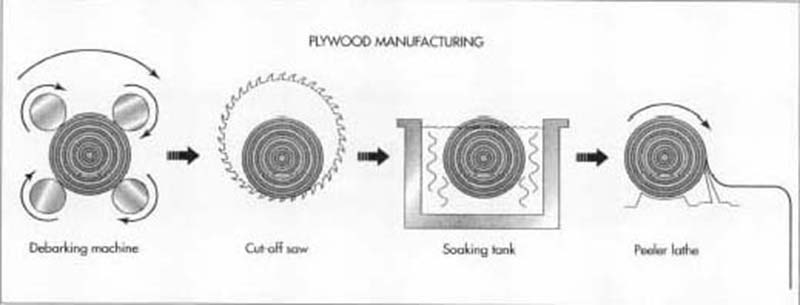
통나무는 먼저 껍질을 벗긴 후 껍질 벗기는 블록으로 자릅니다. 블록을 베니어 조각으로 자르려면 먼저 물에 담가둔 후 껍질을 벗겨 조각으로 만듭니다.
1. 특정 지역에서 선별된 나무는 베어낼 준비가 되었다고 표시됩니다. 벌목은 가솔린 동력 체인톱이나 펠러라고 하는 바퀴 달린 차량 앞에 장착된 대형 유압 가위를 사용하여 수행됩니다. 쓰러진 나무의 가지는 체인톱을 사용하여 제거합니다.
2. 다듬어진 나무줄기, 즉 통나무는 스키더(skidder)라고 불리는 바퀴 달린 차량에 실려 적재 구역으로 운반됩니다. 통나무는 길이에 맞게 잘려 트럭에 실려 합판 공장으로 운반됩니다. 합판 공장에서는 통나무 데크(log deck)라고 불리는 긴 더미에 쌓입니다.
3. 통나무가 필요하면 고무 타이어 로더를 이용하여 통나무 갑판에서 집어 올려 체인 컨베이어에 실어 껍질 제거기로 옮깁니다. 이 기계는 날카로운 톱니가 있는 연삭 휠이나 고압 물을 분사하여 나무껍질을 제거하는 동시에 통나무를 긴 축을 중심으로 천천히 회전시킵니다.
4. 껍질이 벗겨진 통나무는 체인 컨베이어를 통해 제재소로 운반되고, 거대한 원형 톱이 통나무를 약 2.5m에서 2.6m 길이의 조각으로 자릅니다. 이 조각들은 표준 2.4m 길이의 판재를 만드는 데 적합합니다. 이렇게 자른 통나무 조각들은 필러 블록(peeler block)이라고 합니다.
5. 베니어를 자르기 전에 필러 블록을 가열하고 담가서 목재를 부드럽게 해야 합니다. 블록은 증기로 가열하거나 뜨거운 물에 담가둘 수 있습니다. 이 과정은 목재 종류, 블록의 직경 및 기타 요인에 따라 12~40시간 정도 소요됩니다.
6. 가열된 필러 블록은 필러 선반으로 이송되어 자동으로 정렬되고 한 번에 하나씩 선반에 공급됩니다. 선반이 블록을 장축을 중심으로 빠르게 회전시키면, 전체 길이의 칼날이 회전하는 블록 표면에서 분당 90~240m(300~800ft)의 속도로 연속적인 베니어 시트를 벗겨냅니다. 블록의 직경이 약 230~305mm(3~4인치)로 줄어들면, 필러 코어라고 하는 남은 목재 조각이 선반에서 배출되고 새로운 필러 블록이 제자리에 공급됩니다.
7. 필러 선반에서 나온 긴 베니어 시트는 즉시 가공되거나, 길고 여러 층으로 된 트레이에 보관되거나 롤에 감겨질 수 있습니다. 어떤 경우든 다음 공정은 베니어를 사용 가능한 너비, 보통 약 1.4m(4피트-6인치)로 절단하여 표준 너비 1.2m(4피트) 합판 시트를 만드는 것입니다. 동시에 광학 스캐너는 허용할 수 없는 결함이 있는 부분을 찾아 잘라내어 표준 너비보다 작은 베니어 조각만 남깁니다.
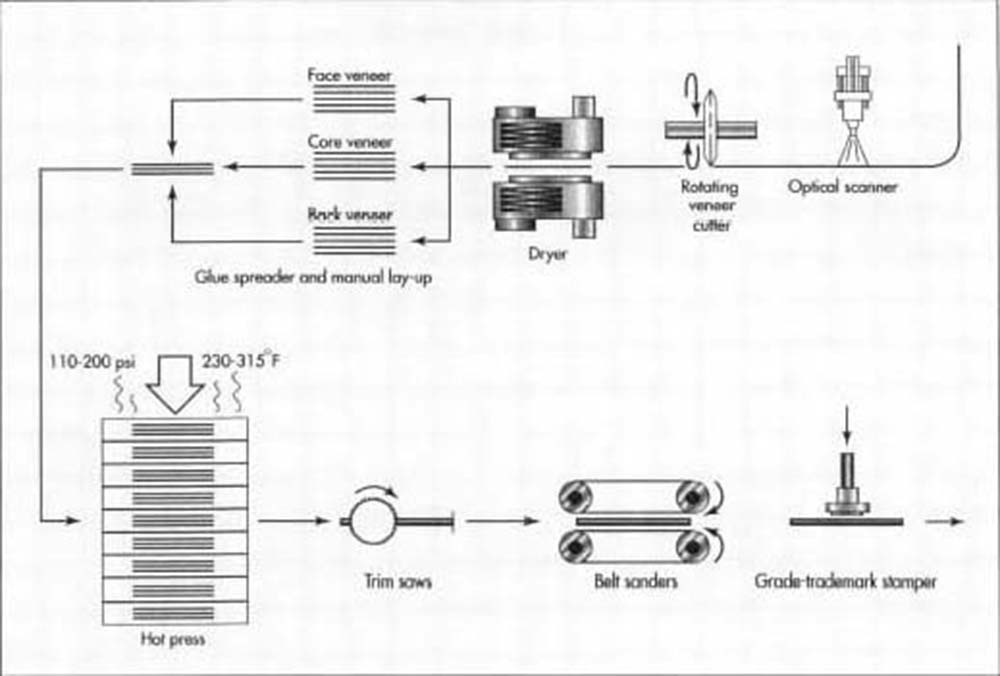
젖은 베니어 조각을 롤 형태로 감는 동안 광학 스캐너가 목재의 허용 불가능한 결함을 감지합니다. 건조된 베니어는 등급을 매겨 쌓아 올립니다. 선택한 베니어 부분을 접착합니다. 열 프레스를 사용하여 베니어를 하나의 단단한 합판으로 접착합니다. 합판은 적절한 등급으로 스탬핑하기 전에 다듬고 사포질합니다.
8. 베니어 조각들을 등급에 따라 분류하고 쌓아 올립니다. 이 작업은 수동으로 진행될 수도 있고, 광학 스캐너를 사용하여 자동으로 진행될 수도 있습니다.
9. 분류된 조각들은 건조기에 투입되어 수분 함량을 줄이고 접착 전에 수축되도록 합니다. 대부분의 합판 공장에서는 조각들이 가열된 챔버를 통해 지속적으로 움직이는 기계식 건조기를 사용합니다. 일부 건조기에서는 건조 속도를 높이기 위해 고속의 가열된 공기를 조각 표면에 분사합니다.
10. 베니어 조각들은 건조기에서 나오면 등급별로 쌓입니다. 폭이 좁은 조각에는 테이프나 접착제로 추가 베니어를 접합하여 외관과 강도가 덜 중요한 내부 층에 사용하기 적합하도록 만듭니다.
11 교차하여 설치될 베니어 부분(3겹 시트의 코어 또는 5겹 시트의 크로스밴드)은 약 4피트-3인치(1.3m) 길이로 절단됩니다.
12 특정 합판 층에 적합한 베니어 부분을 조립하면, 조각들을 쌓아 올리고 접착하는 과정이 시작됩니다. 이 작업은 수동 또는 기계를 이용한 반자동으로 수행될 수 있습니다. 가장 간단한 3겹 합판의 경우, 뒷면 베니어를 평평하게 놓고 접착제 도포기를 통과시켜 윗면에 접착제 층을 도포합니다. 그런 다음, 코어 베니어의 짧은 부분을 접착된 뒷면 위에 가로로 놓고, 전체 시트를 접착제 도포기에 다시 한 번 통과시킵니다. 마지막으로, 앞면 베니어를 접착된 코어 위에 놓고, 프레스에 들어갈 다른 시트들과 함께 겹쳐 쌓습니다.
13 접착된 시트는 여러 개의 구멍이 있는 핫 프레스에 넣습니다. 프레스는 한 번에 20~40장의 시트를 처리할 수 있으며, 각 시트는 별도의 슬롯에 넣어집니다. 모든 시트가 장착되면 프레스는 약 110~200psi(7.6~13.8bar)의 압력으로 시트를 압착하는 동시에 약 230~315°F(109.9~157.2°C)의 온도로 가열합니다. 이 압력은 베니어 층 사이의 좋은 접촉을 보장하고, 열은 접착제가 최대 강도를 위해 적절히 경화되도록 합니다. 2~7분 후 프레스를 열고 시트를 꺼냅니다.
14. 거친 판재는 톱 세트를 통과하여 최종 너비와 길이로 다듬어집니다. 고급 판재는 1.2m 너비의 벨트 샌더 세트를 통과하여 앞면과 뒷면을 모두 샌딩합니다. 중간 등급 판재는 거친 부분을 정리하기 위해 수동으로 부분 샌딩합니다. 일부 판재는 원형 톱날 세트를 통과하여 합판 표면에 얕은 홈을 파서 질감을 부여합니다. 최종 검사 후 남아 있는 결함은 모두 수리합니다.
15. 완성된 시트에는 구매자에게 노출 등급, 등급, 밀 번호 및 기타 요소에 대한 정보를 제공하는 등급 상표가 찍힙니다. 동일한 등급 상표가 있는 시트는 함께 묶인 후 창고로 이동하여 배송을 기다립니다.
목재와 마찬가지로 완벽한 합판이라는 것은 없습니다. 모든 합판에는 어느 정도 결함이 있습니다. 이러한 결함의 수와 위치에 따라 합판 등급이 결정됩니다. 건설용 및 산업용 합판의 표준은 미국 국립표준국(National Bureau of Standards)과 미국 합판협회(American Plywood Association)에서 제정한 제품 표준 PS1에 의해 정의됩니다. 경재 및 장식용 합판의 표준은 미국 국립표준협회(ANSI)와 경재합판제조업협회(Hardwood Plywood Manufacturers' Association)에서 제정한 ANSIIHPMA HP에 의해 정의됩니다. 이러한 표준은 합판의 등급 체계를 확립할 뿐만 아니라, 구조, 성능 및 적용 기준을 명시합니다.
합판은 나무를 상당히 효율적으로 활용합니다. 즉, 나무를 분해하고 다시 조립하여 더 튼튼하고 사용하기 편리한 형태로 만드는 것입니다. 하지만 제조 과정에서 여전히 상당한 폐기물이 발생합니다. 대부분의 경우, 나무 한 그루의 사용 가능한 목재량의 약 50~75%만이 합판으로 가공됩니다. 이 수치를 개선하기 위해 여러 가지 신제품이 개발되고 있습니다.
새로운 제품 중 하나는 배향성 스트랜드 보드(OSB)인데, 통나무에서 베니어를 벗겨내고 심재를 버리는 대신 통나무 전체를 여러 가닥으로 잘게 찢는 방식으로 만들어집니다. 가닥들을 접착제와 혼합하여 나무결이 한 방향으로 향하도록 겹겹이 압축합니다. 이렇게 압축된 겹겹이 합판처럼 서로 직각으로 배열되어 접착됩니다. OSB는 합판만큼 강하고 가격도 약간 저렴합니다.
게시 시간: 2021년 8월 10일